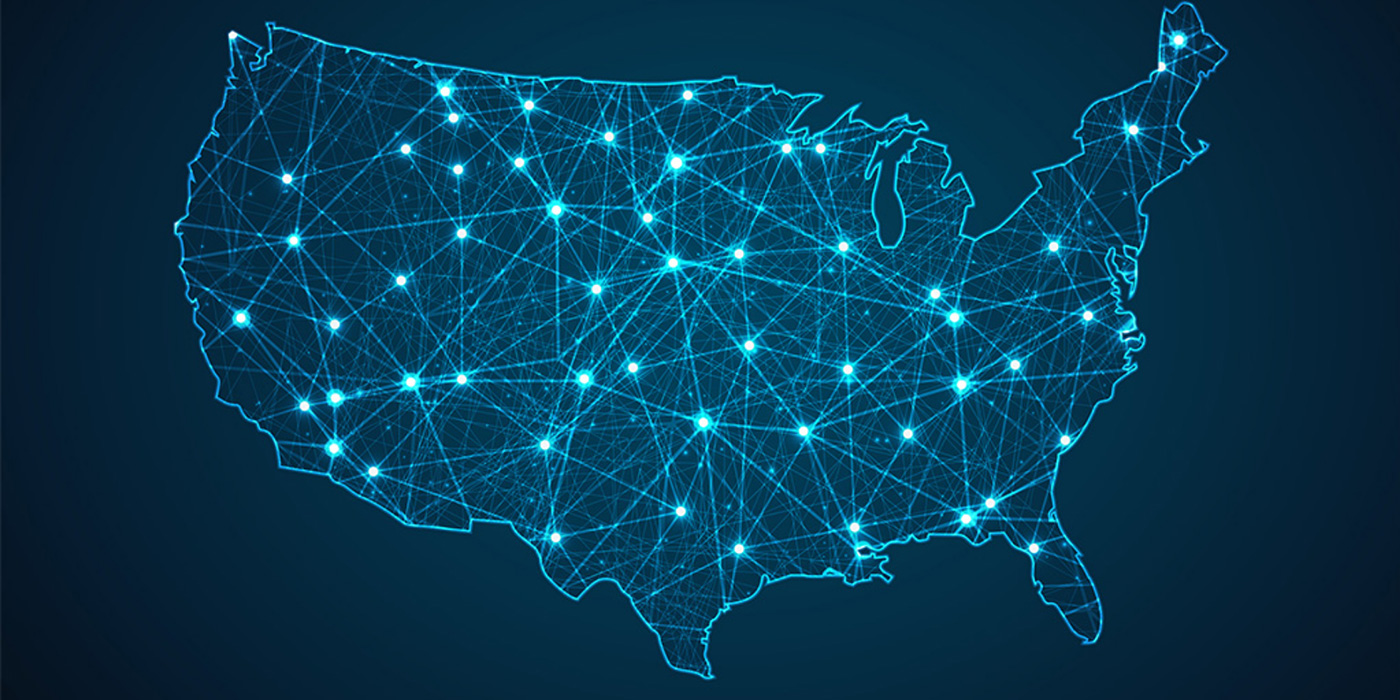
17 Jan Low-cost Sustainable NextGen Batteries will Drive the Future of 21st Century e-mobility
The Global Battery Race Challenge
Our world was transformed in the last three decades by the invention of the lithium battery. In 2019 the World Economic Forum wrote a paper stating, in effect, that the li-ion battery (LIB) was key in saving planet Earth from the cataclysmic impacts from fossil fuel pollution.
Over the past 10 years China has positioned itself to dominate the global Electric Vehicle (EV) and EV battery industries. Chinese automaker BYD’s worldwide EV sales overtook Tesla last quarter, underscoring the rapid progress Chinese EV OEMs made in capturing EV demand beyond China. Global EV sales growth was up 5% last quarter, for a total of 2.5m EV sales, across 55 markets. In an effort to export its large inventory of EVs China has begun construction of 170 ocean cargo ships capable of carrying EVs to ports worldwide.
Low-cost Sustainable Energy Storage is the Key Enabler
The 21st Century global grid electrification powered by renewables and e-mobility in the U.S. and elsewhere, is now becoming uncertain, giving cause to reconsider strategies. For U.S. and global battery and EV OEMs and investors, the financial investment risk with the rise of China EV and battery dominance is now more difficult to quantify. It’s become a real technical and supply chain challenge for any EV and battery OEM to competitively produce batteries needed to store power in e-mobility products such as EVs and consumer devices.
There is no doubt that the U.S. has fallen way behind China in the competition to lead the global EV battery market, particularly those powered by lithium-ion battery materials and cells. Today China controls more than 80% of the battery materials supply chain and half of all batteries built in the world, with CATL accounting for over one-third of global production.
A new focus for U.S. EV OEMs is on developing alternative high-performance battery materials and technologies which could be more cost-effective than LIBs from China. With the right government policies and national focus, the U.S. could reestablish itself as a leader in the next phase of the global e-mobility battery technology transition. Although it’s unlikely that the U.S. will overtake China in lithium-ion battery production, the U.S. might be able to leapfrog China by pioneering superior, abundant, lower-cost battery materials.
The linchpin of U.S. made Next Generation e-mobility batteries are the development of sustainable domestic sourced critical materials with AI driven automated cell production that can replace current Li-ion mined and expensive batteries and materials entirely.
Although industry analysts agree China’s lead in LIBs is far too great for the U.S. to catch up with, however, there are a few potential emerging alternative battery technologies, such as sodium-ion, lithium-sulfur, and solid-state batteries that could disrupt the battery industry.
Although there are some promising claims of these materials now, the challenge is putting it all together in a single cell, without compromising trade-offs inherent in new materials. Achieving the ideal battery technology combination will take 3 to 5 years of development. Because of the U.S. govt. incentives, the most innovative period for breakthrough e-mobility battery technologies is just beginning in the U.S. and will run for the next 10 years or so.
If these emerging technologies can be commercialized from 2025 to 2035, we could see a $35 per kilowatt-hour (kWh) NA-ion-Sulfur-Solid-State battery cell that’s capable of fast charging, 4-10,000+ cycles, a 20 year calendar life, and produced using renewable energy with sustainable abundant raw materials and byproducts found from all around the world.
From 2025 to mid-century, these new generation battery technologies will need to scale at a rate and to a size the world has rarely seen, as we will need tremendous amounts of batteries and sustainable materials to meet the massive demand for these products. This transformative vision will be driven by the U.S. and global electrification of homes, businesses, and transportation. This will require a growth of global battery production from 20 GWh per year from pre-EV days to 2,000+ GWh per year by 2030, and 30,000+ GWh per year for a world with renewables-based global energy and transportation system by 2050.
The global NextGen battery transformation will be powered not by policy but by better technology, products, and economics. Strong national technology and manufacturing policies can help accelerate the change though, as well as create long-term structural
economic benefits. The future of battery storage innovation will come in two main forms – new non-mined critical raw materials and battery manufacturing process innovations.
Novel, commercial processes to manufacture abundant domestic Sulfur (S) and Sodium (NA) active electrode materials at industrial scales will push down cell production cost. In addition to new Sulfur (S) and Sodium (NA) materials, new solid-state electrolyte materials will allow for safer higher energy density cell development and AI automated production.
A Paradigm Shift in Low-Cost Sustainable Energy Storage Batteries
The global push for sustainable energy solutions has intensified the search for next generation material and batteries with higher energy densities, safety, and cost effectiveness. While lithium-sulfur (Li−S) batteries have garnered significant attention because of their very high energy density, their issues with the polysulfide-shuttle effects and reliance on lithium metal anodes introduces challenges such as dendrite growth,
safety risks, low cycle life and supply chain vulnerabilities. Sodium, being abundant, cost effective, and exhibiting suitable electrochemical properties, presents an attractive alternative. A room-temperature sodium-ion anode paired with a sulfur cathode in a sodium-sulfur (NA-S) hybrid-solid-state battery represents a revolutionary approach to address these limitations, enabling a Paradigm Shift in Sustainable Low-Cost Energy Storage Batteries for Next Generation e-mobility battery applications.
Addressing Key Challenges to Develop a NA−S Solid-State Battery a. Dendrite Growth and Safety Risks:
High-capacity Lithium-metal anodes are prone to dendrite formation during repeated cycling, leading to short circuits and safety hazards. By replacing lithium-metal with a sodium-ion (dry) anode, NA−S Solid-State Batteries would eliminate dendrite formation, while enhancing safety and extending cycle life.
Lithium Supply Chain Issues:
The increasing demand for lithium has strained its global supply chain, resulting in price volatility and geopolitical dependencies. Sodium, on the other hand, is globally abundant and cost-effective, making it a more sustainable choice.
Polysulfide Shuttle Effect:
The dissolution of lithium polysulfides in liquid electrolytes has been a persistent challenge in Li−S and NA batteries. Solid-state sulfide-based electrolytes will help prevent this Li-S shuttle effect, ensuring more stable cycling and improved overall performance.
Advantages of NA−S Solid-State Battery
Energy Density:
Sodium-sulfur (NA-S) SS batteries leverage the high theoretical capacity of sulfur (1672 mAh/g) and the improved volumetric efficiency of solid-state electrolyte architectures. By optimizing sodium-ion (dry) anodes and sulfur (dry) cathodes, the NA-S SS battery can achieve energy densities comparable to or exceeding traditional LIB and/or Li−S batteries.
Safety:
The use of solid sulfide electrolytes (Ampcera) not only mitigates the risks of dendrite growth but also eliminates flammable organic liquid electrolytes, significantly improving battery safety. Sodium’s inherently stable plating behavior further enhances reliability.
Cycle Life:
Sodium-ion (dry) anodes exhibit superior cycling stability compared to lithium metal. Combined with the non-reactive nature of sulfide-based solid electrolytes at interfaces, NA-S SS batteries promise longer cycle life than Li−S, Li-metal and/or LIB alternatives.
Cost-Effectiveness:
The reliance on sodium instead of lithium, coupled with sulfur’s abundance and the scalable synthesis of sulfide-based solid electrolytes, positions NA-S SS Batteries as a very low-cost solution. A target cost of $35/kWh is achievable by using low-cost abundant cathode and anode materials and optimizing manufacturing processes with AI software.
Competitive Analysis
Metric NA-SSS Li−S Battery Conventional Sodium-Ion Energy Density (Wh/kg) 350–450 350–500 160–200
Cost ($/kWh) 40–60 100–150 80–120
Safety Excellent Moderate Good
Cycle Life (cycles) >4000 100–800 1000–3000
Supply Chain Dependence Low (Na, S) Med (Li, S) Low (Na)
Innovations for NA-S SS Battery Development
Sulfide-Based Solid Electrolytes:
Sulfide-based solid electrolytes exhibit high ionic conductivity and excellent compatibility with sodium-ion anodes. Optimizing their composition and architecture is critical for NA-S SS Battery’ success.
Interfacial Engineering:
Addressing interfacial challenges, particularly at the cathode/solid electrolyte and anode/solid electrolyte interfaces, is vital. Coatings and graded architectures can minimize resistance and enhance ionic transport.
Scalable AI Automated Manufacturing:
Advances in automated AI based manufacturing lines, such as dry electrode and roll-to-roll processing for solid-state components, will enable cost reductions and commercialization.
Outlook
An NA-S SS Battery with a room-temperature sodium-ion (dry) anode and Li-S cathode presents an unmatched opportunity to develop a next-generation battery system that combines safety, high energy density, long cycle life, and low cost. By addressing the challenges faced by Li−S batteries and capitalizing on the advantages of sodium, NA-S Solid-State battery platform could redefine the global energy storage landscape and achieve the ambitious cost target of $35/kWh, making them an attractive viable solution for widespread adoption in electric vehicles, consumer devices, grid storage, and beyond.
Conclusion and Market Reality
It’s unlikely that any country outside of China, even Korea, and Japan, will be able to compete in the LIB race. Only if the U.S. can develop sustainable batteries that are substantially better and competitive on a $/kWh basis, will U.S. OEMs be able to take the lead in the Nextgen battery race to reach GWh scale battery production in the next decade. As challenging as the technical hurdles are to leapfrog China’s LIB cell and material manufacturing dominance, new NA-S Solid-state battery materials are now being developed and production of these materials are being scaled for U.S. giga-factories.
The United Nations Industrial Development Organization predicts that by 2030 China will account for nearly 45% of all global manufacturing. By 2030, China could be responsible for approximately 40%-50% of global CO2 emissions from coal factories, which translates to 6-7.5 billion metric tons annually, which defeats the purpose of renewables and EVs.
What is clear is that the world needs to shift to renewable energy to make better and cheaper batteries to store that energy. If enterprising entrepreneurs, scientists and engineers in the U.S. and elsewhere find ways to overcome the technical and sustainable materials supply chain challenges and drive the NextGen battery cell price down from $70/kWh to $35/kWh, then this global EV and battery industry paradigm shift will happen. This will be a collaborative private/govt. effort, powered by 24/7 renewable energy to mitigate the impacts of Climate Change, enabling a global e-mobility Industrial Revolution.